Garage Floor Epoxy Cost: How much is it?
When it comes to sprucing up our garages, one question often pops up: “How much does garage floor epoxy cost?” It’s a fair ask, especially when we’re watching our budgets. Let’s break down those numbers, factor in some often-overlooked considerations, and get you the info you need.
Why Consider Epoxy for Your Garage Floor?
Epoxy not only gives your garage a sleek, professional look, but it’s also super durable. It’s completely resistant of oil stains and water damage, making those accidental spills a breeze to clean up. Plus, with its longevity, you won’t be re-doing the floor anytime soon. Practical and pretty? That’s a win-win!
Factors That Influence Epoxy Flooring Cost
Size of Your Garage
Square Footage: Naturally, the larger the area to be covered, the more material will be required. An average one-car garage might be around 250 square feet, while a two-car garage typically ranges from 400 to 500 square feet. Larger garages or those with unusual layouts might require even more epoxy.
Shape and Layout: Simple, rectangular garages might be straightforward to work on. However, those with multiple corners, pillars, or recessed areas might demand more time and precision, potentially increasing labor costs.
Complexity of Application
Floor Condition: A floor in poor condition, with cracks, pits, or unevenness, requires more preparation before epoxy application. This can entail filling cracks, smoothing surfaces, or even grinding the entire floor.
Previous Coatings: Existing paint, sealers, or older epoxy layers can affect the new application. Removal of these layers or ensuring compatibility can add to the project’s complexity and cost.
Design Preferences: A plain, single-color epoxy application is generally less complicated than intricate patterns, multiple colors, or decorative flake additions.
Features and Enhancements: Options such as anti-slip additives, UV stabilizers for sunlight protection, or self-leveling properties can add to the material costs and potentially the application complexity.
Region and Market Dynamics
Labor Rates: Depending on your location, labor costs can fluctuate significantly. Urban areas or regions with a high cost of living might naturally have higher labor rates compared to more rural regions.
Material Availability: In some areas, specific epoxy brands or types might be readily available and cheaper, while others might need to be ordered in, affecting both price and delivery time.
Local Demand: In regions where epoxy flooring is trendy, there might be a surge in demand, leading to higher prices. Conversely, lower demand can sometimes translate to discounts or promotions.
Local Climate: In areas with significant temperature fluctuations, there might be a preference for particular types of epoxy that can withstand these changes. This can affect both material availability and pricing.
Additional Factors
Brand and Quality of Epoxy: Established, high-quality brands might come with a premium price tag, while lesser-known or lower-quality options might be cheaper but may not provide the same durability or finish.
Project Timeline: If you’re looking for a fast turnaround, you might need to pay a premium for expedited services.
Warranties or Guarantees: Professionals who offer longer warranties or satisfaction guarantees might charge more, reflecting the confidence in their work and the quality of materials used.
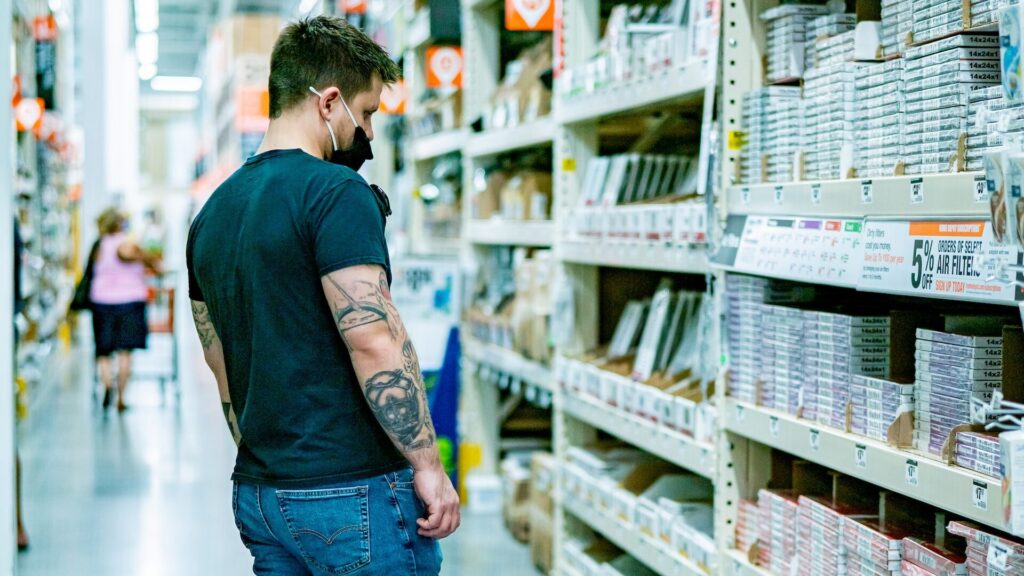
Material Costs
When selecting an epoxy for your garage floor, the material cost isn’t just about the raw price per gallon or per square foot. Here’s a breakdown of the key aspects of material costs:
Type of Epoxy
Solid Epoxy: Comprising 100% epoxy, this is the highest-quality option. It’s exceptionally durable, provides a robust and thick coat, and tends to be the most expensive among the three primary types.
Water-based Epoxy: A more diluted form, it acts more like a sealer than a traditional epoxy. Though it’s easier to apply and generally less expensive than solid epoxy, it might not provide the same level of protection and longevity.
Solvent-based Epoxy: Sitting between solid and water-based, this epoxy offers a good balance of durability and ease of application. Its price typically falls in the mid-range.
Quality and Features
UV Resistance: Epoxies with UV stabilizers or resistance can prevent yellowing or discoloration when exposed to sunlight, but they may come at a premium.
Thickness: High-quality epoxies tend to be denser, providing a thicker layer, which can impact cost.
Self-leveling: Some epoxies come with self-leveling features, offering a smoother finish without additional effort.
Additives and Enhancements
Anti-slip Additives: Especially crucial for garage floors that might get wet, these provide additional grip but can add to the cost.
Decorative Flakes or Chips: Adding a decorative element to your floor, these can elevate the visual appeal but also the price.
Color Pigments: If you’re looking for a specific shade or custom color, you might need to spend extra.
Brand Reputation
Established and well-reviewed brands might have higher prices due to their track record of quality and durability. Off-brands or lesser-known options might be more affordable but could compromise on quality or longevity.
Packaging and Size
Bulk Buying: Purchasing epoxy in larger quantities or for significant areas can sometimes offer savings on a per-square-foot basis.
Kit vs. Individual Components: Some brands offer epoxy kits that include everything you need for application, like primers, base coats, and top coats. These kits might seem more expensive upfront, but they can offer value for money and ease of selection.
Shipping and Handling: For those who order epoxy online, consider shipping costs, especially for bulk orders. Some suppliers might offer free shipping for orders over a specific amount, while others could charge based on weight and distance.
Labor Costs
Floor Preparation
Cleaning: Before any epoxy application, the floor needs thorough cleaning. This might involve power washing, degreasing, or removing any previous coatings.
Concrete Repairs: Cracks, pits, and other imperfections in the concrete should be repaired to ensure a smooth application. Depending on the floor’s condition, this step can range from minor patchwork to more extensive repairs.
Grinding or Acid Etching: To achieve better adhesion, the concrete surface often needs roughening. Grinding with a diamond grinder or acid etching are common methods. Grinding tends to be more expensive but provides a superior surface for epoxy bonding.
Epoxy Application
Primer Application: Some floors might require a primer before the epoxy layer, ensuring better adhesion and longevity.
Main Coat: The actual epoxy application varies in complexity based on the product type and floor condition. Professionals use specialized tools and techniques to guarantee an even spread without air bubbles.
Top Coat or Sealant: To protect the epoxy and provide a finished look, a top coat or sealant might be applied. This adds another layer of labor and time.
Specialized Techniques or Designs
Decorative Designs: If you’re looking for a decorative finish, such as patterns or multi-colored designs, this will require additional time and skill.
Use of Additives: Incorporating anti-slip additives or decorative flakes evenly can be time-consuming.
Labor Rates
Regional Variations: The cost of labor can vary widely based on your location. Urban areas or regions with a higher cost of living might have higher labor rates.
Professional Experience: Established professionals with a strong reputation might charge a premium for their services, but they often bring expertise, reliability, and better results.
Project Duration
Overnight Projects: Some professionals might offer quicker turnaround times by working extended hours or overnight, but this could come at a premium.
Multiple Layer: If your floor requires multiple epoxy layers or coats, it will extend the project duration, increasing labor costs.
Additional Services
Warranty or Maintenance Plans
Some professionals offer post-application services, such as periodic check-ups or warranties. While this might increase initial costs, it can offer peace of mind and long-term savings.
Waste Disposal
After the project, there might be waste materials, like used containers or cleaning agents. Proper disposal can sometimes incur additional costs.
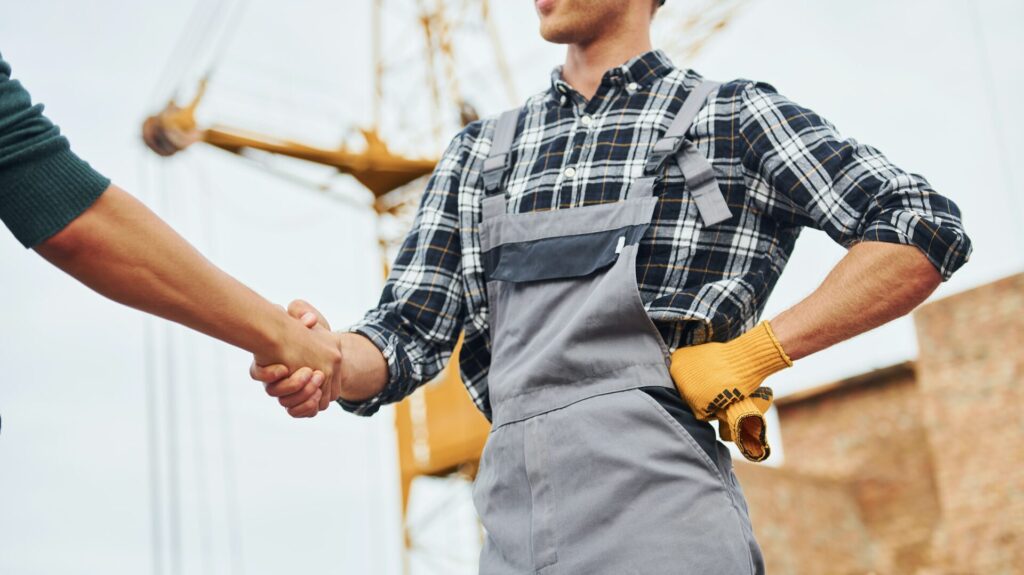
DIY vs. Hiring a Professional
Skill Level and Experience
DIY: Undertaking an epoxy project requires a certain level of skill. If you have experience with similar home improvement projects or have a knack for detailed tasks, DIY might be feasible. However, if it’s your first time, there’s a steep learning curve.
Professional: They bring expertise, knowledge of best practices, and often have tackled a range of challenges, ensuring the final result is of high quality.
Cost
DIY: You save on labor costs, which can be significant. However, you might end up spending more on tools or materials, especially if mistakes are made. Additionally, there’s the potential cost of time – the project might take longer than anticipated.
Professional: While you’ll pay more upfront, professionals often have access to wholesale material prices, specialized equipment, and can complete the job faster. Plus, many offer warranties, which can save money in the long run.
Equipment and Tools
DIY: You’ll need to purchase or rent essential equipment, like concrete grinders or acid etching materials, and protective gear. This can add to the project’s cost and requires knowledge to use effectively.
Professional: They come equipped with all the necessary tools and materials, ensuring the job is done right the first time.
Quality and Durability
DIY: While many homeowners achieve excellent results, the risk of imperfections, such as air bubbles, uneven application, or issues with bonding, is higher. Mistakes can affect the floor’s durability and appearance.
Professional: With their experience and expertise, professionals tend to provide a more consistent and durable finish.
Time Commitment
DIY: Beyond the actual application, consider the time needed for research, shopping for materials, floor prep, and any potential rework.
Professional: They often provide a more accurate timeline for project completion, allowing you to plan accordingly.
Potential Risks
DIY: There’s the risk of incorrect material selection, inadequate floor prep, or improper application. Additionally, without proper ventilation or protective gear, working with certain chemicals can pose health risks.
Professional: They’re trained to handle materials safely, ensure adequate ventilation, and minimize health and application risks.
Learning Opportunity vs. Peace of Mind
DIY: For many, the challenge and satisfaction of learning a new skill and seeing a project through from start to finish can be rewarding.
Professional: Hiring an expert offers peace of mind. You can be confident in the quality of the work and often have the backing of a warranty.
How much does Garage Floor Epoxy Cost?
The cost of epoxy flooring for an average-sized garage can vary based on numerous factors, such as regional pricing variations, the quality of materials chosen, and the specific conditions of the garage floor. For this estimate, we’ll use an average-sized two-car garage, which is typically around 400-500 square feet.
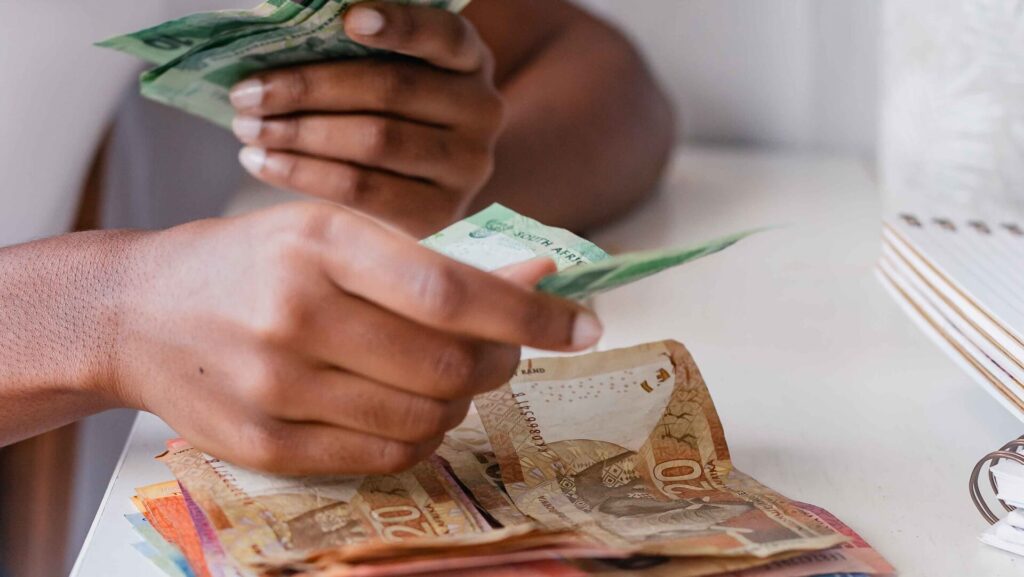
DIY Cost Estimate
Material Costs | Labor Costs |
Epoxy kits suitable for a two-car garage: $250 to $600 | Since it’s DIY, the labor cost would be $0 in monetary terms, but there’s the time investment to consider. $0 |
Cleaning & Prep Supplies: Including degreasers, concrete patch, acid etch or rental for a grinder: $50 – $150 | |
Additional Supplies: Brushes, rollers, mixing tools, protective gear, etc: $40 – $80 | |
Total DIY Cost (Materials + Labor): $340 – $830 |
Professional Cost Estimate
Material Costs | Labor Costs |
As professionals often get materials at wholesale prices, they might get a slight discount. However, they’ll use higher-end products for durability. Estimate: $300 – $700 | Floor Preparation: Grinding, cleaning, and repairs can range from $1 to $3 per square foot: $400 – $1200 for 400 sq. ft. |
Epoxy Application: Labor for the actual application can range from $3 to $5 per square foot: $1200 – $2000 for 400 sq. ft. | |
Total Professional Costs: (Materials + Labor): $1900 – $3900 |
Final Estimates
DIY: $340 – $830
Professional: $1900 – $3900
Remember, these are rough estimates. The actual costs can vary based on regional labor rates, the condition of the garage floor, the specific epoxy product selected, and other variables. Always gather multiple quotes from professionals and research product reviews before making a decision.
Conclusion
Epoxy flooring costs for your garage aren’t just about size. They’re shaped by the floor’s condition, design choices, and even local market trends. For many, a garage is more than just car storage – it’s a vital part of the home. Knowing the factors that impact the cost helps you budget smartly. Whether you go DIY or hire professionals, remember: sometimes you get what you pay for. Focus on a mix of cost, quality, and functionality. A good epoxy job can make your garage both useful and attractive.
FAQs
1. Why does the condition of my garage floor affect the epoxy application cost?
The condition of the garage floor directly impacts the amount of preparation needed before epoxy application. Cracks, pits, or uneven surfaces require filling, smoothing, or grinding, which adds to labor and material costs. A well-maintained floor, on the other hand, may need minimal prep, reducing expenses.
2. Is it more cost-effective to choose a DIY approach over hiring professionals for epoxy flooring?
While DIY might save on labor costs, there are additional considerations like equipment rentals, potential for mistakes, and the time investment. Professionals, with their expertise, may offer higher quality work and access to better material pricing. Each option has its pros and cons, so it’s essential to assess individual comfort, skills, and budget.
3. How can regional market dynamics influence garage floor epoxy cost?
Your location can play a role in both labor and material costs. Urban areas or places with a high cost of living might have higher labor rates. The availability of specific epoxy brands, local demand, and even the local climate can affect material choices, availability, and pricing.
4. Are there additional costs associated with decorative or intricate epoxy flooring designs?
Yes, intricate patterns, multiple colors, or the addition of decorative flakes can increase material and labor costs. Such designs may require more time, specialized products, or skilled techniques to achieve the desired look and finish.
5. Why might some professionals charge more for epoxy flooring installation?
Professionals who use high-quality brands, offer extended warranties, or guarantee satisfaction might have higher rates. Their prices often reflect their confidence in their work, the quality of materials used, and the added assurance they provide to customers.
Comments are closed.